Are you gearing up for an interview for a Oxyacetylene Cutter position? Whether you’re a seasoned professional or just stepping into the role, understanding what’s expected can make all the difference. In this blog, we dive deep into the essential interview questions for Oxyacetylene Cutter and break down the key responsibilities of the role. By exploring these insights, you’ll gain a clearer picture of what employers are looking for and how you can stand out. Read on to equip yourself with the knowledge and confidence needed to ace your next interview and land your dream job!
Acing the interview is crucial, but landing one requires a compelling resume that gets you noticed. Crafting a professional document that highlights your skills and experience is the first step toward interview success. ResumeGemini can help you build a standout resume that gets you called in for that dream job.
Essential Interview Questions For Oxyacetylene Cutter
1. What are the different types of oxyacetylene cutting torches and their applications?
Oxyacetylene cutting torches are classified into three main types based on their design and application:
- Hand-held torches: These are lightweight and portable, suitable for manual cutting operations in various industries, including construction, shipbuilding, and automotive repairs.
- Machine-mounted torches: These are designed for automated cutting processes in manufacturing environments, where precise and repetitive cutting operations are required.
- Underwater torches: These specialized torches are used for underwater cutting applications, such as marine salvage, pipeline maintenance, and offshore construction.
2. Explain the process of setting up an oxyacetylene cutting system and the safety precautions to be taken.
Setting up an oxyacetylene cutting system involves the following steps:
Pre-Setup Safety Precautions
- Ensure proper ventilation to prevent gas accumulation.
- Wear appropriate safety gear, including fire-resistant clothing, gloves, and eye protection.
- Inspect equipment for damage or leaks and replace any faulty components.
Setup Procedure
- Connect the oxygen and acetylene cylinders to the regulator and torch.
- Adjust the regulators to the desired gas pressures.
- Check for leaks by applying soapy water to all connections.
- Ignite the torch and adjust the flame to a neutral setting.
3. How do you determine the correct cutting tip size for a given material thickness?
Selecting the appropriate cutting tip size is crucial for efficient and safe cutting. The following factors should be considered:
- Material thickness: The tip size should be slightly larger than the material thickness to ensure proper preheating and cutting.
- Material type: Different materials require different tip sizes due to varying thermal conductivity and melting points.
- Cutting speed and quality: Larger tips allow for faster cutting speeds but may produce rougher cuts. Smaller tips offer better cut quality but slower cutting speeds.
4. Describe the different cutting techniques and when to use each one.
The two main cutting techniques in oxyacetylene cutting are:
- Straight cutting: Used for cutting straight lines and shapes, where the torch is moved along the desired path while maintaining a perpendicular angle to the surface.
- Bevel cutting: Used to create beveled edges for welding or joining purposes. The torch is tilted at an angle to the surface, resulting in a sloped cut.
5. How do you adjust the oxyacetylene flame for different materials and cutting conditions?
Adjusting the oxyacetylene flame is essential for achieving optimal cutting performance. The following parameters are adjusted:
- Oxygen-to-acetylene ratio: This ratio controls the flame temperature and shape. A neutral flame (equal proportions of oxygen and acetylene) is suitable for most materials. An oxidizing flame (excess oxygen) is used for cutting thicker materials, while a carburizing flame (excess acetylene) is used for cutting thin or non-ferrous materials.
- Flame length: The flame length should be approximately 1.5 times the material thickness. A shorter flame provides better cut quality but may result in poor preheating. A longer flame ensures proper preheating but can lead to slag formation.
6. What are the common defects that can occur in oxyacetylene cutting and how can they be prevented?
Common defects in oxyacetylene cutting include:
- Dross: Slag or oxide buildup on the cut surface, resulting from insufficient oxygen supply.
- Gouging: Excessive penetration or melting of the material, caused by an oxidizing flame or too high a cutting speed.
- Kerf taper: A wider cut at the bottom than at the top, indicating improper torch angle or tip size.
- Warping: Distortion of the material due to excessive heat input. This can be prevented by using a smaller tip size and faster cutting speed.
7. How do you maintain and troubleshoot an oxyacetylene cutting system?
Regular maintenance and troubleshooting ensure optimal performance and safety of the cutting system:
- Clean and inspect equipment regularly: Remove any debris or slag buildup from the torch, tips, and hoses.
- Check for leaks: Use soapy water to identify and tighten any loose connections.
- Replace worn or damaged parts: Inspect tips, hoses, and regulators regularly for signs of wear or damage.
- Troubleshoot common problems: Address issues such as poor flame quality, backfiring, or clogged tips by checking gas pressures, cleaning components, or replacing faulty parts.
8. Explain how to cut different types of materials using an oxyacetylene torch, such as steel, aluminum, and stainless steel.
Cutting different materials requires specific adjustments:
- Steel: Use a neutral flame with a slight excess of oxygen. Select the appropriate tip size based on material thickness.
- Aluminum: Use a carburizing flame with a slight excess of acetylene. Aluminum melts at a lower temperature, so a smaller tip size and faster cutting speed are recommended.
- Stainless steel: Use a neutral flame with a slight excess of oxygen. Stainless steel requires a higher preheating temperature, so a larger tip size and slower cutting speed may be necessary.
9. How do you ensure safety while working with an oxyacetylene cutting system?
Safety is paramount when working with oxyacetylene equipment:
- Wear proper protective gear: Flame-resistant clothing, gloves, eye protection, and hearing protection.
- Ventilate the work area: Prevent gas accumulation and ensure adequate oxygen levels.
- Handle cylinders safely: Secure cylinders upright, use proper regulators, and open valves slowly to avoid bursts.
- Follow safe lighting and extinguishing procedures: Use a striker or spark lighter to ignite the torch. Extinguish the flame by closing the acetylene valve first, then the oxygen valve.
- Never point the torch at people or flammable materials: Sparks and flames can cause serious injuries or fires.
10. How do you stay up-to-date with the latest best practices and advancements in oxyacetylene cutting technology?
To stay current in the field:
- Attend industry workshops and conferences: Learn about new techniques, equipment, and safety regulations.
- Read trade publications and technical articles: Stay informed about industry trends and best practices.
- Consult with manufacturers and experts: Seek guidance from industry professionals for specific questions or advice.
- Participate in online forums and discussions: Engage with peers and experts to share knowledge and learn from others.
- Obtain industry certifications: Demonstrate your skills and knowledge by pursuing recognized certifications in oxyacetylene cutting.
Interviewers often ask about specific skills and experiences. With ResumeGemini‘s customizable templates, you can tailor your resume to showcase the skills most relevant to the position, making a powerful first impression. Also check out Resume Template specially tailored for Oxyacetylene Cutter.
Career Expert Tips:
- Ace those interviews! Prepare effectively by reviewing the Top 50 Most Common Interview Questions on ResumeGemini.
- Navigate your job search with confidence! Explore a wide range of Career Tips on ResumeGemini. Learn about common challenges and recommendations to overcome them.
- Craft the perfect resume! Master the Art of Resume Writing with ResumeGemini’s guide. Showcase your unique qualifications and achievements effectively.
- Great Savings With New Year Deals and Discounts! In 2025, boost your job search and build your dream resume with ResumeGemini’s ATS optimized templates.
Researching the company and tailoring your answers is essential. Once you have a clear understanding of the Oxyacetylene Cutter‘s requirements, you can use ResumeGemini to adjust your resume to perfectly match the job description.
Key Job Responsibilities
An oxyacetylene cutter is a skilled professional responsible for cutting and shaping metal using an oxyacetylene torch. Their key responsibilities typically include the following:
1. Cutting and Shaping Metals
Using an oxyacetylene torch, oxyacetylene cutters cut and shape metal according to specifications and blueprints. They ensure precision and accuracy in their cuts and maintain high-quality standards in the finished products.
2. Operating and Maintaining Equipment
Oxyacetylene cutters are proficient in operating and maintaining oxyacetylene torches, regulators, and other related equipment. They regularly inspect and clean their equipment to ensure optimal performance and safety.
3. Reading and Interpreting Blueprints and Drawings
To cut and shape metal accurately, oxyacetylene cutters need to be able to read and interpret blueprints and drawings. They must understand the dimensions, tolerances, and other specifications to ensure the final product meets the required standards.
4. Following Safety Procedures
Working with oxyacetylene torches requires strict adherence to safety procedures. Oxyacetylene cutters must be familiar with and comply with all safety guidelines to prevent accidents and ensure the well-being of themselves and others in the workplace.
Interview Tips
Preparing thoroughly for an oxyacetylene cutter interview can significantly increase your chances of success. Here are some tips and hacks to help you ace the interview:
1. Research the Company and Position
Take the time to research the company you are applying to, as well as the specific oxyacetylene cutter position. This will give you a good understanding of their business, values, and what they are looking for in a candidate.
2. Practice Your Answers
Prepare for common interview questions, such as “Tell me about yourself” and “Why are you interested in this role?” Practice your answers out loud to gain confidence and ensure they are clear and concise.
3. Showcase Your Skills and Experience
Highlight your relevant skills and experience, such as your proficiency in operating oxyacetylene torches, reading blueprints, and maintaining equipment. Provide specific examples of your work to demonstrate your abilities.
4. Emphasize Safety Awareness
Emphasize your understanding of and commitment to safety procedures. Explain how you prioritize safety in your work and provide examples of how you have followed safety protocols in previous roles.
5. Ask Informed Questions
Asking thoughtful questions at the end of the interview shows your interest and engagement. Prepare questions about the company, the role, or the industry to demonstrate your curiosity and desire to learn more.
Next Step:
Now that you’re armed with the knowledge of Oxyacetylene Cutter interview questions and responsibilities, it’s time to take the next step. Build or refine your resume to highlight your skills and experiences that align with this role. Don’t be afraid to tailor your resume to each specific job application. Finally, start applying for Oxyacetylene Cutter positions with confidence. Remember, preparation is key, and with the right approach, you’ll be well on your way to landing your dream job. Build an amazing resume with ResumeGemini
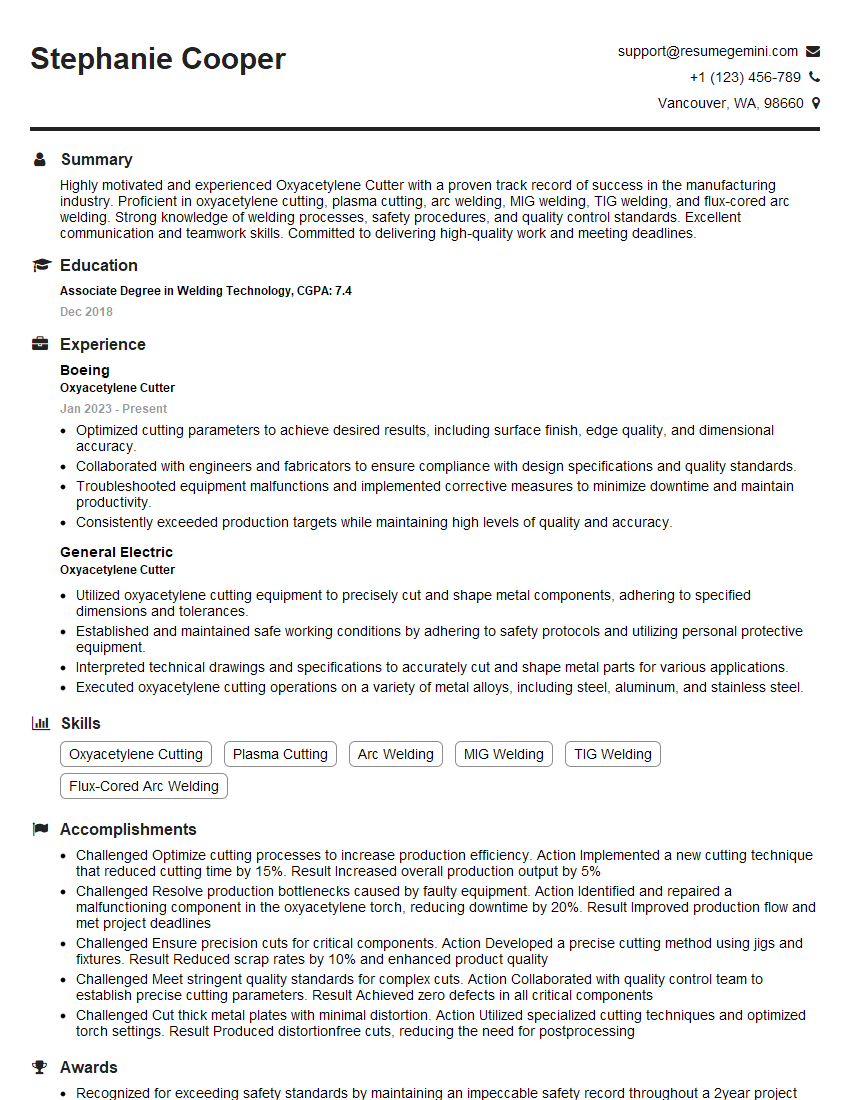