Are you gearing up for an interview for a Production Tool Engineer position? Whether you’re a seasoned professional or just stepping into the role, understanding what’s expected can make all the difference. In this blog, we dive deep into the essential interview questions for Production Tool Engineer and break down the key responsibilities of the role. By exploring these insights, you’ll gain a clearer picture of what employers are looking for and how you can stand out. Read on to equip yourself with the knowledge and confidence needed to ace your next interview and land your dream job!
Acing the interview is crucial, but landing one requires a compelling resume that gets you noticed. Crafting a professional document that highlights your skills and experience is the first step toward interview success. ResumeGemini can help you build a standout resume that gets you called in for that dream job.
Essential Interview Questions For Production Tool Engineer
1. Explain the design process of a plastic injection mould?
The design process of a plastic injection mould involves several key steps:
- Part Design: Analyzing the part design to determine the mould’s overall shape and dimensions.
- Mould Base Selection: Choosing an appropriate mould base based on part size, complexity, and production requirements.
- Gating System Design: Determining the type and location of the gates to ensure proper melt flow and part filling.
- Cooling System Design: Designing cooling channels to control the cooling rate of the plastic part, preventing warpage or defects.
- Ejection System Design: Creating a mechanism to eject the part from the mould cleanly and efficiently.
2. How do you optimize the cooling system of an injection mould?
Material Selection:
- Choosing materials with high thermal conductivity, such as beryllium copper or aluminum.
Channel Design:
- Using conformal cooling channels that follow the part’s contours.
- Optimizing channel diameter and spacing for efficient heat transfer.
Flow Control:
- Utilizing baffles or flow restrictors to ensure uniform cooling throughout the part.
- Balancing flow rates to prevent hot spots or overcooling.
3. Discuss the factors that affect the selection of mould materials?
- Type of Plastic: Different plastics have varying temperature and chemical resistance requirements.
- Mould Complexity: More complex moulds may require specialized materials for durability.
- Production Volume: High-volume moulds require materials with exceptional wear resistance.
- Cost and Availability: The budget and availability of materials must be considered.
- Machinability and Finish: The material should be easy to machine and provide the desired surface finish.
4. How do you troubleshoot a plastic injection moulding defect, such as sink marks?
- Identify the Cause: Determine the underlying cause of the sink marks, such as insufficient cooling or material shrinkage.
- Adjust Process Parameters: Modify injection speed, pressure, or cooling time to improve melt flow and prevent sink marks.
- Modify Mould Design: Optimize cooling channels, gate location, or part thickness to reduce stress concentrations.
- Use Additives: Consider adding fillers or modifiers to the plastic material to improve its flowability or reduce shrinkage.
5. Explain the different types of mould vents and their purposes?
- Direct Vents: Channels cut directly into the mould surface to release trapped air during filling.
- Sprue Vents: Vents located in the sprue or runners to allow air to escape before entering the mould cavity.
- Surface Vents: Small, shallow vents cut into the part surface to release air from recessed areas.
- Vacuum Vents: Vents connected to a vacuum system to actively remove air during filling.
6. Describe the importance of runner balancing in injection moulding?
- Uniform Melt Flow: Runner balancing ensures that plastic flows evenly into all mould cavities, preventing part defects.
- Reduced Cycle Time: By optimizing flow, runner balancing can shorten the overall injection cycle time.
- Improved Part Quality: Balanced runners minimize pressure variations, leading to consistent part dimensions and reduced warpage.
7. Explain the concept of conformal cooling in injection mould design?
Conformal cooling involves designing cooling channels that follow the contours of the plastic part. This allows for:
- Optimized Cooling: Channels are positioned closer to the part surface, providing efficient heat transfer.
- Reduced Cycle Time: Faster cooling enables shorter cycle times.
- Improved Part Quality: Conformal cooling minimizes thermal stresses, reducing part warpage and defects.
8. How do you determine the appropriate gate size and location for an injection mould?
- Part Geometry: The gate size and location should ensure proper filling of the part without creating excessive flow resistance.
- Material Properties: Different plastics have varying flow characteristics, which influence gate design.
- Mouldability: The gate should be designed to minimize part defects, such as weld lines or jetting.
- Production Volume: High-volume production requires gates that can deliver material quickly and efficiently.
9. Explain the different types of injection moulding machines and their applications?
- Hydraulic Machines: Provide precise control and high clamping force, ideal for large, complex parts.
- Toggle Machines: Offer a mechanical advantage for high-speed, high-volume production.
- Electric Machines: Energy-efficient and precise, suitable for smaller parts or complex geometries.
- Hybrid Machines: Combine hydraulic and electric systems for optimal performance and energy savings.
10. How do you stay up-to-date with the latest trends and technologies in plastic injection moulding?
- Industry Conferences: Attend industry events and conferences to learn about new developments.
- Trade Publications: Read industry magazines and articles to stay informed.
- Online Resources: Utilize websites, webinars, and online training platforms.
- Collaboration with Suppliers: Engage with mould makers and material suppliers for insights and updates.
Interviewers often ask about specific skills and experiences. With ResumeGemini‘s customizable templates, you can tailor your resume to showcase the skills most relevant to the position, making a powerful first impression. Also check out Resume Template specially tailored for Production Tool Engineer.
Career Expert Tips:
- Ace those interviews! Prepare effectively by reviewing the Top 50 Most Common Interview Questions on ResumeGemini.
- Navigate your job search with confidence! Explore a wide range of Career Tips on ResumeGemini. Learn about common challenges and recommendations to overcome them.
- Craft the perfect resume! Master the Art of Resume Writing with ResumeGemini’s guide. Showcase your unique qualifications and achievements effectively.
- Great Savings With New Year Deals and Discounts! In 2025, boost your job search and build your dream resume with ResumeGemini’s ATS optimized templates.
Researching the company and tailoring your answers is essential. Once you have a clear understanding of the Production Tool Engineer‘s requirements, you can use ResumeGemini to adjust your resume to perfectly match the job description.
Key Job Responsibilities
Production Tool Engineers play a crucial role in manufacturing, and their key responsibilities include:
1. Tool and Die Design
Design, develop and evaluate tools, dies and fixtures throughout the product lifecycle.
2. Equipment Maintenance and Troubleshooting
Maintain, calibrate and troubleshoot production equipment, including tooling and dies.
3. Process Development and Improvement
Develop and improve production processes to increase efficiency, reduce costs and enhance product quality.
4. Automation and Optimization
Automate production processes using robotics and other systems to improve efficiency and reduce cycle times.
Interview Tips
To ace a Production Tool Engineer interview, consider the following tips:
1. Research the Company and Role
Thoroughly research the company and specific role to understand their needs and requirements.
2. Highlight Relevant Experience
Highlight your experience in tool and die design, equipment maintenance, process improvement and automation.
3. Showcase Technical Skills
Demonstrate your proficiency in CAD/CAM software, manufacturing processes and quality control techniques.
4. Emphasize Teamwork and Communication
Emphasize your ability to work effectively in a team environment and communicate technical concepts clearly.
Next Step:
Now that you’re armed with the knowledge of Production Tool Engineer interview questions and responsibilities, it’s time to take the next step. Build or refine your resume to highlight your skills and experiences that align with this role. Don’t be afraid to tailor your resume to each specific job application. Finally, start applying for Production Tool Engineer positions with confidence. Remember, preparation is key, and with the right approach, you’ll be well on your way to landing your dream job. Build an amazing resume with ResumeGemini
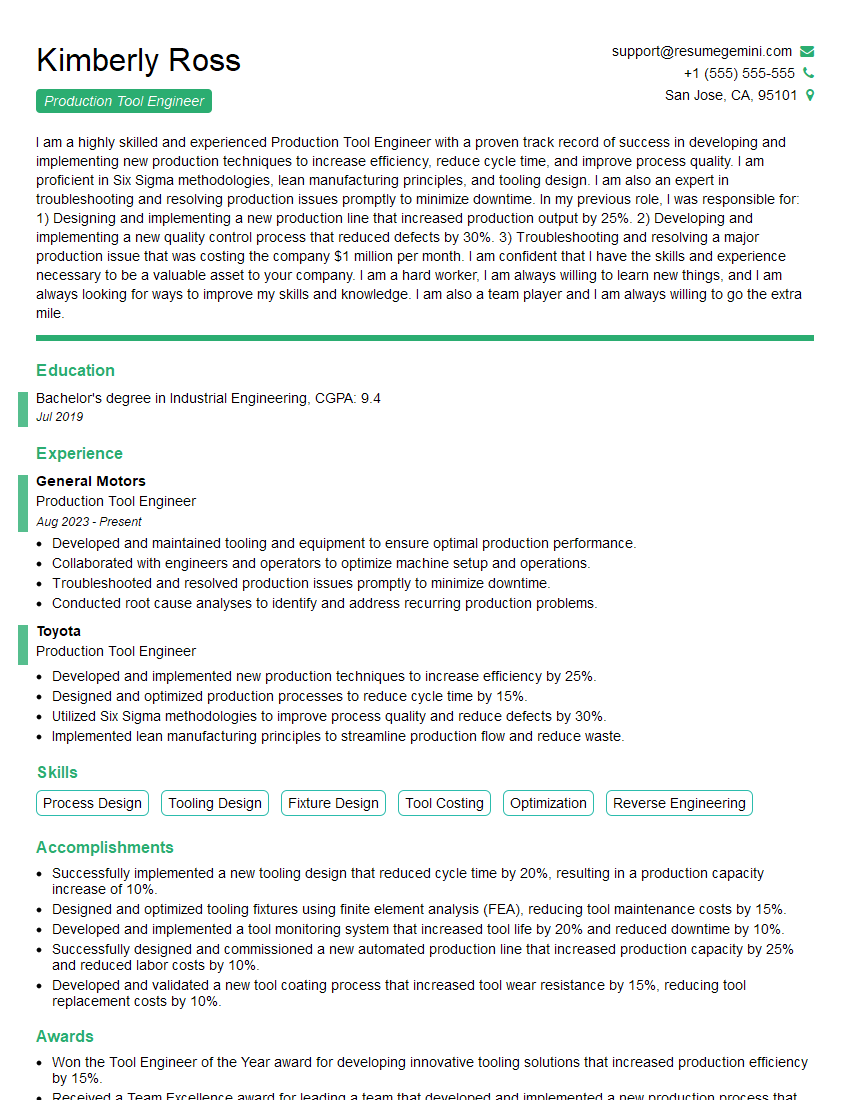