Ever felt underprepared for that crucial job interview? Or perhaps you’ve landed the interview but struggled to articulate your skills and experiences effectively? Fear not! We’ve got you covered. In this blog post, we’re diving deep into the Superintendent, Maintenance, Managerial interview questions that you’re most likely to encounter. But that’s not all. We’ll also provide expert insights into the key responsibilities of a Superintendent, Maintenance, Managerial so you can tailor your answers to impress potential employers.
Acing the interview is crucial, but landing one requires a compelling resume that gets you noticed. Crafting a professional document that highlights your skills and experience is the first step toward interview success. ResumeGemini can help you build a standout resume that gets you called in for that dream job.
Essential Interview Questions For Superintendent, Maintenance, Managerial
1. How do you ensure the smooth operation of all maintenance activities, including preventive maintenance, corrective maintenance, and capital projects?
In terms of preventive maintenance, I establish a comprehensive schedule based on industry best practices and equipment manufacturer recommendations. This schedule includes tasks such as regular equipment inspections, lubrication, and filter changes. For corrective maintenance, I promptly address any equipment breakdowns or malfunctions, minimizing downtime and ensuring efficient operations. As for capital projects, I collaborate with engineering and construction teams to plan, execute, and commission new or upgraded facilities and systems, ensuring they meet operational requirements and regulatory compliance.
2. What strategies do you employ to optimize maintenance costs and improve operational efficiency?
Cost Optimization
- Implement predictive maintenance techniques to identify potential issues before they become major failures, reducing unexpected repairs and downtime.
- Negotiate favorable contracts with suppliers and vendors for materials and equipment, ensuring competitive pricing and cost savings.
- Establish a rigorous inventory management system to minimize waste and optimize stock levels, reducing carrying costs.
Operational Efficiency
- Utilize computerized maintenance management systems (CMMS) to streamline work orders, track asset performance, and enhance communication among maintenance teams.
- Implement lean manufacturing principles to eliminate waste and streamline processes, improving productivity and reducing response times.
- Promote cross-training and skills development for maintenance technicians, ensuring they have the versatility to handle a wide range of tasks efficiently.
3. How do you stay up-to-date with industry best practices and technological advancements in maintenance?
I actively participate in industry conferences, seminars, and workshops to stay informed about emerging technologies and maintenance strategies. I subscribe to industry publications and engage in online forums to connect with other maintenance professionals and learn from their experiences. Additionally, I regularly seek opportunities for professional development and certifications to enhance my knowledge and skills.
4. Describe your approach to managing a team of maintenance technicians and fostering a positive and productive work environment.
I believe in empowering my team and creating a culture of accountability and collaboration. I clearly define roles and responsibilities, ensuring each technician understands their tasks and expectations. I provide regular training and support to enhance their skills and ensure they have the necessary tools and resources to perform their jobs effectively. I foster open communication and encourage my team to share ideas and feedback, creating a positive and supportive work environment.
5. What are your key performance indicators (KPIs) for maintenance operations, and how do you track and measure them?
- Mean Time to Repair (MTTR): Measures the average time it takes to diagnose and fix equipment issues, indicating the efficiency of maintenance response.
- Mean Time Between Failures (MTBF): Indicates the reliability of equipment and the effectiveness of preventive maintenance.
- Maintenance Cost per Unit: Assesses the cost-effectiveness of maintenance operations, considering labor, materials, and equipment.
- Overall Equipment Effectiveness (OEE): A comprehensive measure that combines availability, performance, and quality to evaluate the effectiveness of maintenance in supporting production targets.
I track these KPIs using a CMMS or other software tools. Regular data analysis allows me to identify areas for improvement and make data-driven decisions to enhance maintenance performance.
6. How do you prioritize maintenance tasks and allocate resources effectively?
I use a risk-based approach to prioritize maintenance tasks. I assess the potential consequences of equipment failure, considering factors such as safety risks, production impact, and financial losses. Based on this assessment, I assign critical tasks with higher priority and allocate resources accordingly. I also consider the availability of spare parts, maintenance history, and the skills required for the task.
7. What is your approach to managing contractor relationships and ensuring their performance meets expectations?
I establish clear contractual agreements with contractors, outlining their responsibilities, performance standards, and reporting requirements. I regularly communicate with contractors, providing them with updates on equipment performance and maintenance needs. I also conduct performance evaluations to assess their adherence to agreed-upon terms and the quality of their work. If necessary, I implement corrective actions or consider alternative contracting options to ensure that their performance meets the required standards.
8. How do you handle unexpected equipment failures or emergencies?
In the event of unexpected equipment failures or emergencies, I respond promptly to minimize downtime and potential safety hazards. I assess the situation, prioritize tasks, and coordinate with the necessary maintenance team and emergency response personnel. I ensure effective communication among stakeholders, keeping them informed about the situation and progress of repairs. I also document the incident thoroughly, including corrective actions taken and lessons learned, to prevent similar occurrences in the future.
9. Describe your experience in managing maintenance budgets and ensuring cost-effective operations.
I have a proven track record of managing maintenance budgets effectively. I work closely with finance and procurement departments to develop realistic maintenance budgets based on historical data, industry benchmarks, and operational requirements. I prioritize maintenance activities based on their impact on production and safety, ensuring cost-effective allocation of resources. I also explore cost-saving opportunities, such as negotiating favorable contracts with vendors, implementing energy-efficient practices, and optimizing inventory levels.
10. How do you collaborate with other departments, such as operations and engineering, to ensure a cohesive approach to maintenance?
I foster strong relationships with other departments, particularly operations and engineering. I participate in cross-functional meetings to discuss maintenance needs, equipment upgrades, and production schedules. This collaboration enables me to align maintenance activities with operational goals and ensure that engineering modifications are incorporated into the maintenance plan. By working together, we optimize resource allocation, minimize production interruptions, and improve overall plant efficiency.
Interviewers often ask about specific skills and experiences. With ResumeGemini‘s customizable templates, you can tailor your resume to showcase the skills most relevant to the position, making a powerful first impression. Also check out Resume Template specially tailored for Superintendent, Maintenance, Managerial.
Career Expert Tips:
- Ace those interviews! Prepare effectively by reviewing the Top 50 Most Common Interview Questions on ResumeGemini.
- Navigate your job search with confidence! Explore a wide range of Career Tips on ResumeGemini. Learn about common challenges and recommendations to overcome them.
- Craft the perfect resume! Master the Art of Resume Writing with ResumeGemini’s guide. Showcase your unique qualifications and achievements effectively.
- Great Savings With New Year Deals and Discounts! In 2025, boost your job search and build your dream resume with ResumeGemini’s ATS optimized templates.
Researching the company and tailoring your answers is essential. Once you have a clear understanding of the Superintendent, Maintenance, Managerial‘s requirements, you can use ResumeGemini to adjust your resume to perfectly match the job description.
Key Job Responsibilities
The Superintendent, Maintenance, Managerial is responsible for overseeing the maintenance and repair of buildings, grounds, and equipment. They work closely with other departments to ensure that all maintenance operations are carried out efficiently and effectively.
1. Plan and Manage Maintenance Operations
The Superintendent develops and implements maintenance plans and procedures. They also oversee the scheduling, coordination, and execution of all maintenance activities. This includes:
- Developing and maintaining a maintenance budget
- Identifying and prioritizing maintenance needs
- Scheduling and overseeing maintenance repairs
- Inspecting buildings and grounds to identify potential maintenance issues
- Developing and implementing preventive maintenance programs
2. Supervise Maintenance Staff
The Superintendent supervises a team of maintenance staff. They are responsible for hiring, training, and motivating their staff. They also ensure that all staff members are adequately trained and equipped to perform their jobs safely and effectively. This includes:
- Hiring and firing maintenance staff
- Providing training and development opportunities for staff
- Setting performance goals and evaluating staff performance
- Ensuring that all staff members are following safety procedures
- Handling grievances and resolving conflicts
3. Manage Maintenance Equipment
The Superintendent is responsible for managing the maintenance equipment used by their staff. This includes purchasing, maintaining, and repairing equipment. They also work with other departments to ensure that the equipment is used safely and efficiently. This includes:
- Purchasing and maintaining maintenance equipment
- Repairing and servicing maintenance equipment
- Ensuring that all equipment is in good working order
- Developing and implementing safety procedures for the use of equipment
- Training staff on the proper use of equipment
4. Manage Maintenance Records
The Superintendent is responsible for maintaining maintenance records. This includes keeping track of all maintenance activities, equipment, and staff. They also work with other departments to ensure that maintenance records are accurate and complete. This includes:
- Maintaining a maintenance log
- Tracking all maintenance costs
- Preparing reports on maintenance activities
- Ensuring that all maintenance records are secure
- Developing and implementing a record-keeping system
Interview Tips
Here are some tips to help you prepare for your interview for a Superintendent, Maintenance, Managerial position:
1. Research the Company and the Position
Before your interview, it is important to research the company and the position. This will help you understand the company’s culture, goals, and needs. You can also use this information to tailor your answers to the interviewer’s questions.
2. Practice Your Answers to Common Interview Questions
There are a number of common interview questions that you are likely to be asked. It is important to practice your answers to these questions so that you can deliver them confidently and effectively. Some common interview questions include:
- Tell me about yourself.
- Why are you interested in this position?
- What are your strengths and weaknesses?
- What are your salary expectations?
3. Bring a Portfolio of Your Work
A portfolio of your work can be a great way to show the interviewer your skills and experience. This could include examples of your maintenance plans, procedures, or reports. You could also include examples of your work in other areas, such as project management or team leadership.
4. Be Prepared to Talk About Your Experience
The interviewer will want to know about your experience in the maintenance field. Be prepared to talk about your experience in detail. This includes your experience in planning and managing maintenance operations, supervising maintenance staff, managing maintenance equipment, and managing maintenance records.
Next Step:
Armed with this knowledge, you’re now well-equipped to tackle the Superintendent, Maintenance, Managerial interview with confidence. Remember, preparation is key. So, start crafting your resume, highlighting your relevant skills and experiences. Don’t be afraid to tailor your application to each specific job posting. With the right approach and a bit of practice, you’ll be well on your way to landing your dream job. Build your resume now from scratch or optimize your existing resume with ResumeGemini. Wish you luck in your career journey!
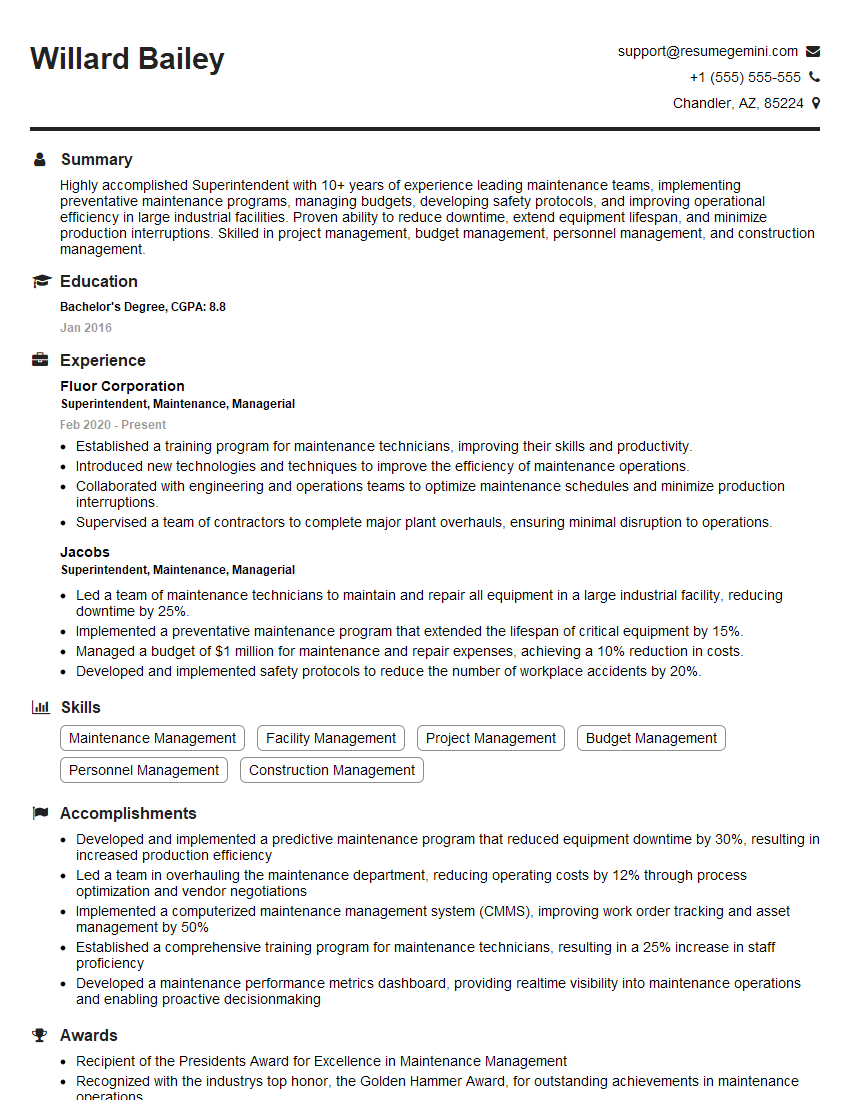