Are you a seasoned Quality Control Supervisor (QC Supervisor) seeking a new career path? Discover our professionally built Quality Control Supervisor (QC Supervisor) Resume Template. This time-saving tool provides a solid foundation for your job search. Simply click “Edit Resume” to customize it with your unique experiences and achievements. Customize fonts and colors to match your personal style and increase your chances of landing your dream job. Explore more Resume Templates for additional options.
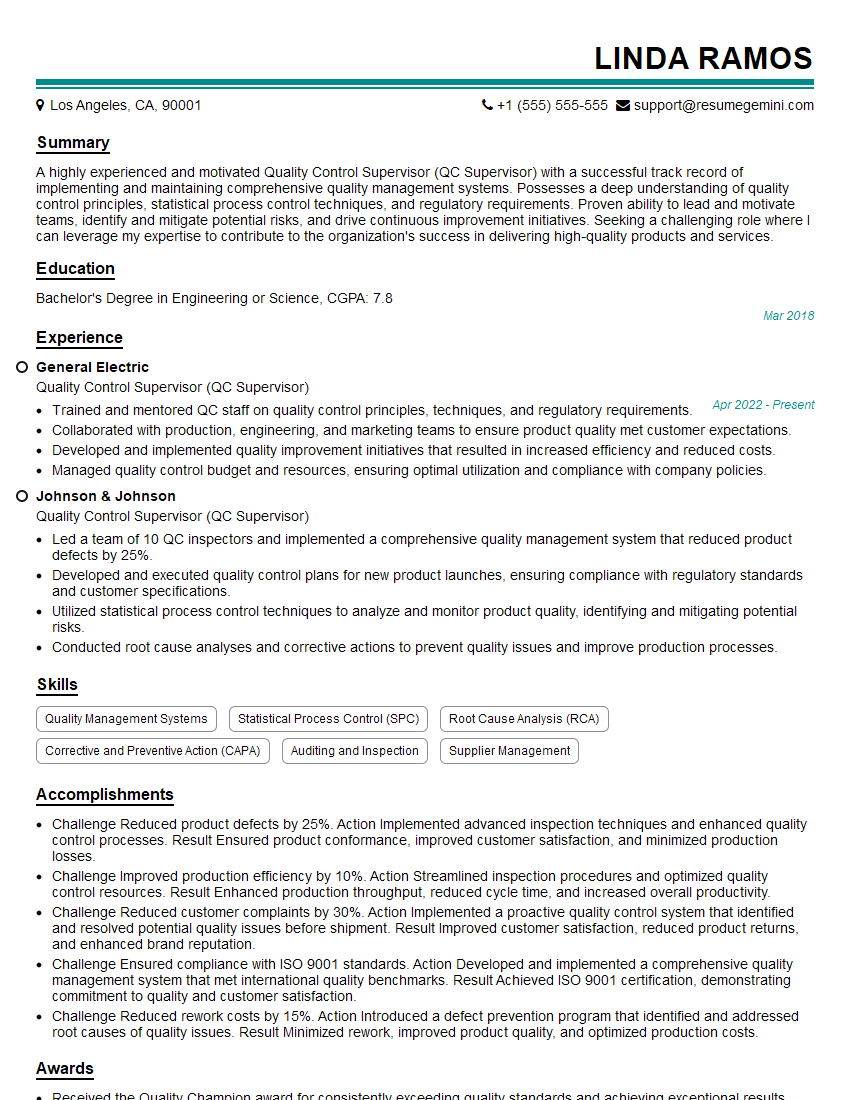
Linda Ramos
Quality Control Supervisor (QC Supervisor)
Summary
A highly experienced and motivated Quality Control Supervisor (QC Supervisor) with a successful track record of implementing and maintaining comprehensive quality management systems. Possesses a deep understanding of quality control principles, statistical process control techniques, and regulatory requirements. Proven ability to lead and motivate teams, identify and mitigate potential risks, and drive continuous improvement initiatives. Seeking a challenging role where I can leverage my expertise to contribute to the organization’s success in delivering high-quality products and services.
Education
Bachelor’s Degree in Engineering or Science
March 2018
Skills
- Quality Management Systems
- Statistical Process Control (SPC)
- Root Cause Analysis (RCA)
- Corrective and Preventive Action (CAPA)
- Auditing and Inspection
- Supplier Management
Work Experience
Quality Control Supervisor (QC Supervisor)
- Trained and mentored QC staff on quality control principles, techniques, and regulatory requirements.
- Collaborated with production, engineering, and marketing teams to ensure product quality met customer expectations.
- Developed and implemented quality improvement initiatives that resulted in increased efficiency and reduced costs.
- Managed quality control budget and resources, ensuring optimal utilization and compliance with company policies.
Quality Control Supervisor (QC Supervisor)
- Led a team of 10 QC inspectors and implemented a comprehensive quality management system that reduced product defects by 25%.
- Developed and executed quality control plans for new product launches, ensuring compliance with regulatory standards and customer specifications.
- Utilized statistical process control techniques to analyze and monitor product quality, identifying and mitigating potential risks.
- Conducted root cause analyses and corrective actions to prevent quality issues and improve production processes.
Accomplishments
- Challenge Reduced product defects by 25%. Action Implemented advanced inspection techniques and enhanced quality control processes. Result Ensured product conformance, improved customer satisfaction, and minimized production losses.
- Challenge Improved production efficiency by 10%. Action Streamlined inspection procedures and optimized quality control resources. Result Enhanced production throughput, reduced cycle time, and increased overall productivity.
- Challenge Reduced customer complaints by 30%. Action Implemented a proactive quality control system that identified and resolved potential quality issues before shipment. Result Improved customer satisfaction, reduced product returns, and enhanced brand reputation.
- Challenge Ensured compliance with ISO 9001 standards. Action Developed and implemented a comprehensive quality management system that met international quality benchmarks. Result Achieved ISO 9001 certification, demonstrating commitment to quality and customer satisfaction.
- Challenge Reduced rework costs by 15%. Action Introduced a defect prevention program that identified and addressed root causes of quality issues. Result Minimized rework, improved product quality, and optimized production costs.
Awards
- Received the Quality Champion award for consistently exceeding quality standards and achieving exceptional results.
- Recognized with the Excellence in Quality Control award for implementing innovative quality initiatives that significantly improved product reliability.
- Awarded the Outstanding Contribution to Quality award for developing a comprehensive quality management system that enhanced operational efficiency.
Certificates
- American Society for Quality (ASQ) Certified Quality Engineer (CQE)
- International Organization for Standardization (ISO) 9001:2015 Lead Auditor
- American Society for Quality (ASQ) Six Sigma Black Belt
- Project Management Professional (PMP)
Career Expert Tips:
- Select the ideal resume template to showcase your professional experience effectively.
- Master the art of resume writing to highlight your unique qualifications and achievements.
- Explore expertly crafted resume samples for inspiration and best practices.
- Build your best resume for free this new year with ResumeGemini. Enjoy exclusive discounts on ATS optimized resume templates.
How To Write Resume For Quality Control Supervisor (QC Supervisor)
- Highlight your technical expertise and experience in quality control management.
- Quantify your accomplishments and provide specific examples of how you have improved product quality.
- Emphasize your leadership and team-building skills.
- Demonstrate your commitment to continuous improvement and staying up-to-date with industry best practices.
- Proofread your resume carefully for errors and ensure that it is well-written and formatted.
Essential Experience Highlights for a Strong Quality Control Supervisor (QC Supervisor) Resume
- Develop and implement quality control plans for new product launches, ensuring compliance with regulatory standards and customer specifications.
- Utilize statistical process control techniques to analyze and monitor product quality, identifying and mitigating potential risks.
- Conduct root cause analyses and corrective actions to prevent quality issues and improve production processes.
- Train and mentor QC staff on quality control principles, techniques, and regulatory requirements.
- Collaborate with production, engineering, and marketing teams to ensure product quality meets customer expectations.
- Develop and implement quality improvement initiatives that resulted in increased efficiency and reduced costs.
- Manage quality control budget and resources, ensuring optimal utilization and compliance with company policies.
Frequently Asked Questions (FAQ’s) For Quality Control Supervisor (QC Supervisor)
What are the key responsibilities of a Quality Control Supervisor?
The key responsibilities of a Quality Control Supervisor include developing and implementing quality control plans, monitoring product quality, conducting root cause analyses, training and mentoring QC staff, collaborating with other departments, and managing quality improvement initiatives.
What are the qualifications required to become a Quality Control Supervisor?
To become a Quality Control Supervisor, you typically need a bachelor’s degree in engineering or a related field, as well as several years of experience in quality control or a related field.
What are the career prospects for a Quality Control Supervisor?
Quality Control Supervisors can advance to management positions, such as Quality Assurance Manager or Director of Quality. They may also move into related fields, such as product development or engineering.
What are the challenges faced by Quality Control Supervisors?
Quality Control Supervisors face a number of challenges, including ensuring product quality, meeting regulatory requirements, and staying up-to-date with industry best practices.
What are the rewards of being a Quality Control Supervisor?
The rewards of being a Quality Control Supervisor include making a positive impact on product quality, protecting consumers, and advancing in your career.
What are the key skills required for a Quality Control Supervisor?
Key skills for a Quality Control Supervisor include quality control principles, statistical process control techniques, root cause analysis, corrective and preventive action, auditing and inspection, and supplier management.