Are you a seasoned Quality Specialist seeking a new career path? Discover our professionally built Quality Specialist Resume Template. This time-saving tool provides a solid foundation for your job search. Simply click “Edit Resume” to customize it with your unique experiences and achievements. Customize fonts and colors to match your personal style and increase your chances of landing your dream job. Explore more Resume Templates for additional options.
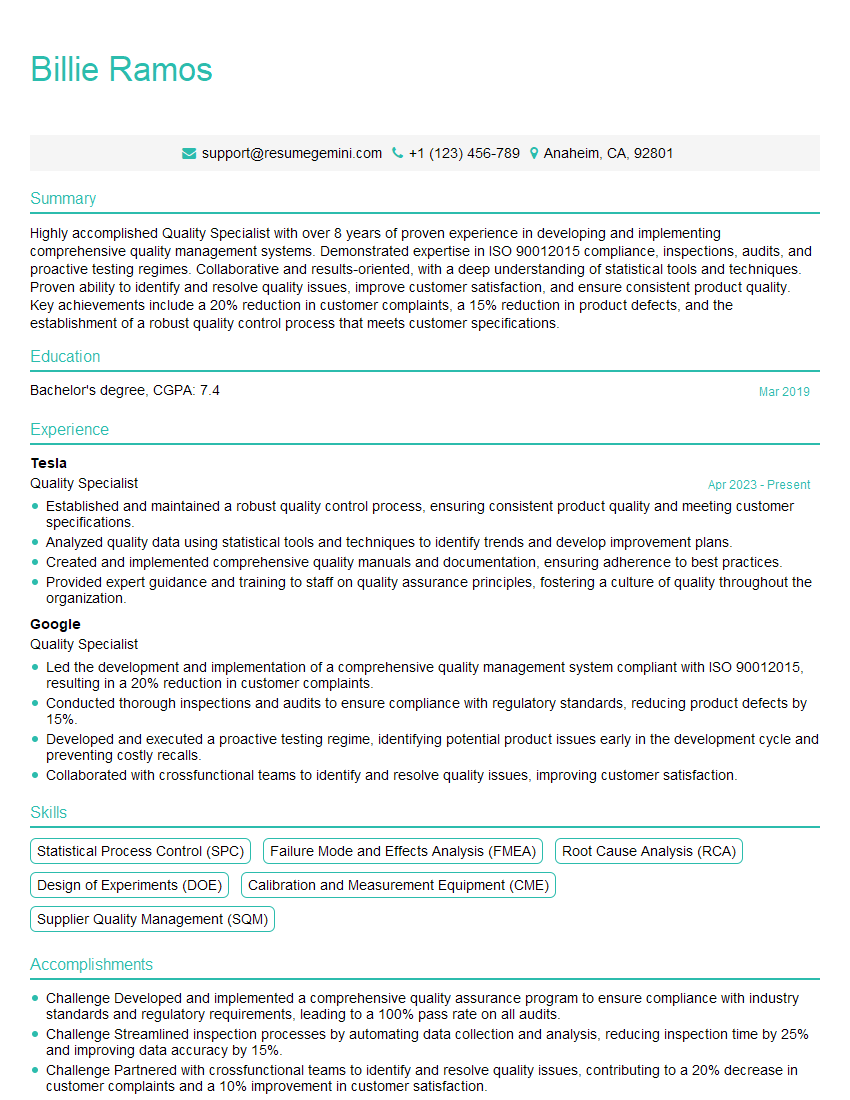
Billie Ramos
Quality Specialist
Summary
Highly accomplished Quality Specialist with over 8 years of proven experience in developing and implementing comprehensive quality management systems. Demonstrated expertise in ISO 90012015 compliance, inspections, audits, and proactive testing regimes. Collaborative and results-oriented, with a deep understanding of statistical tools and techniques. Proven ability to identify and resolve quality issues, improve customer satisfaction, and ensure consistent product quality.
Key achievements include a 20% reduction in customer complaints, a 15% reduction in product defects, and the establishment of a robust quality control process that meets customer specifications.
Education
Bachelor’s degree
March 2019
Skills
- Statistical Process Control (SPC)
- Failure Mode and Effects Analysis (FMEA)
- Root Cause Analysis (RCA)
- Design of Experiments (DOE)
- Calibration and Measurement Equipment (CME)
- Supplier Quality Management (SQM)
Work Experience
Quality Specialist
- Established and maintained a robust quality control process, ensuring consistent product quality and meeting customer specifications.
- Analyzed quality data using statistical tools and techniques to identify trends and develop improvement plans.
- Created and implemented comprehensive quality manuals and documentation, ensuring adherence to best practices.
- Provided expert guidance and training to staff on quality assurance principles, fostering a culture of quality throughout the organization.
Quality Specialist
- Led the development and implementation of a comprehensive quality management system compliant with ISO 90012015, resulting in a 20% reduction in customer complaints.
- Conducted thorough inspections and audits to ensure compliance with regulatory standards, reducing product defects by 15%.
- Developed and executed a proactive testing regime, identifying potential product issues early in the development cycle and preventing costly recalls.
- Collaborated with crossfunctional teams to identify and resolve quality issues, improving customer satisfaction.
Accomplishments
- Challenge Developed and implemented a comprehensive quality assurance program to ensure compliance with industry standards and regulatory requirements, leading to a 100% pass rate on all audits.
- Challenge Streamlined inspection processes by automating data collection and analysis, reducing inspection time by 25% and improving data accuracy by 15%.
- Challenge Partnered with crossfunctional teams to identify and resolve quality issues, contributing to a 20% decrease in customer complaints and a 10% improvement in customer satisfaction.
- Challenge Developed and executed a vendor quality assurance program to assess and qualify new suppliers, reducing incoming defective materials by 15%.
- Challenge Implemented a process improvement methodology to identify and eliminate nonvalueadded activities, resulting in a 25% reduction in cycle time and a 10% increase in productivity.
Awards
- Recognized for exceptional contributions to ISO 9001 certification and process improvement initiatives, leading to a 15% reduction in nonconformances and a 35% increase in customer satisfaction.
- Awarded the Quality Excellence Award for implementing a comprehensive statistical process control system, resulting in a 20% improvement in product quality and a 10% reduction in production costs.
- Recognized as a Six Sigma Black Belt for successfully completing multiple quality improvement projects, leading to significant cost savings and process enhancements.
Certificates
- Certified Quality Engineer (CQE)
- Certified Quality Inspector (CQI)
- Certified Six Sigma Black Belt (CSSBB)
- Certified Manager of Quality/Operational Excellence (CMQ/OE)
Career Expert Tips:
- Select the ideal resume template to showcase your professional experience effectively.
- Master the art of resume writing to highlight your unique qualifications and achievements.
- Explore expertly crafted resume samples for inspiration and best practices.
- Build your best resume for free this new year with ResumeGemini. Enjoy exclusive discounts on ATS optimized resume templates.
How To Write Resume For Quality Specialist
- Highlight your experience in developing and implementing ISO 90012015 compliant quality management systems.
- Quantify your achievements with specific metrics, such as reductions in customer complaints and product defects.
- Showcase your expertise in statistical process control, failure mode and effects analysis, root cause analysis, and design of experiments.
- Emphasize your ability to collaborate effectively with cross-functional teams and build strong relationships with customers.
- Demonstrate your commitment to continuous improvement and your passion for quality excellence.
Essential Experience Highlights for a Strong Quality Specialist Resume
- Developing and implementing quality management systems compliant with ISO standards, ensuring compliance with regulatory requirements
- Conducting thorough inspections and audits to ensure adherence to quality standards and customer specifications
- Developing and executing proactive testing regimes to identify potential product issues early in the development cycle
- Collaborating with cross-functional teams to identify and resolve quality issues, fostering a culture of quality within the organization
- Analyzing quality data using statistical tools and techniques to identify trends, develop improvement plans, and monitor progress
- Creating and implementing comprehensive quality manuals and documentation, ensuring adherence to best practices and industry standards
Frequently Asked Questions (FAQ’s) For Quality Specialist
What are the key skills and responsibilities of a Quality Specialist?
Key skills include statistical process control, failure mode and effects analysis, root cause analysis, design of experiments, calibration and measurement equipment, and supplier quality management. Responsibilities include developing and implementing quality management systems, conducting inspections and audits, analyzing quality data, and resolving quality issues.
What are the career prospects for Quality Specialists?
Quality Specialists are in high demand in a wide range of industries, including manufacturing, healthcare, and pharmaceuticals. They can advance to management positions, such as Quality Manager or Director of Quality Assurance.
What is the average salary for a Quality Specialist?
The average salary for a Quality Specialist in the United States is around $75,000 per year, according to Salary.com.
What are the educational requirements for a Quality Specialist?
Most Quality Specialists have a bachelor’s degree in a related field, such as engineering, science, or business. Some employers may also require certification from the American Society for Quality (ASQ).
What is the difference between a Quality Specialist and a Quality Inspector?
Quality Specialists are responsible for developing and implementing quality management systems, while Quality Inspectors are responsible for conducting inspections and audits to ensure that products and processes meet quality standards.
What is the role of a Quality Specialist in ISO 90012015 compliance?
Quality Specialists play a critical role in helping organizations achieve and maintain ISO 90012015 compliance. They are responsible for developing and implementing quality management systems that meet the requirements of the standard, as well as conducting internal audits to ensure compliance.