Are you a seasoned Veneer Clipper seeking a new career path? Discover our professionally built Veneer Clipper Resume Template. This time-saving tool provides a solid foundation for your job search. Simply click “Edit Resume” to customize it with your unique experiences and achievements. Customize fonts and colors to match your personal style and increase your chances of landing your dream job. Explore more Resume Templates for additional options.
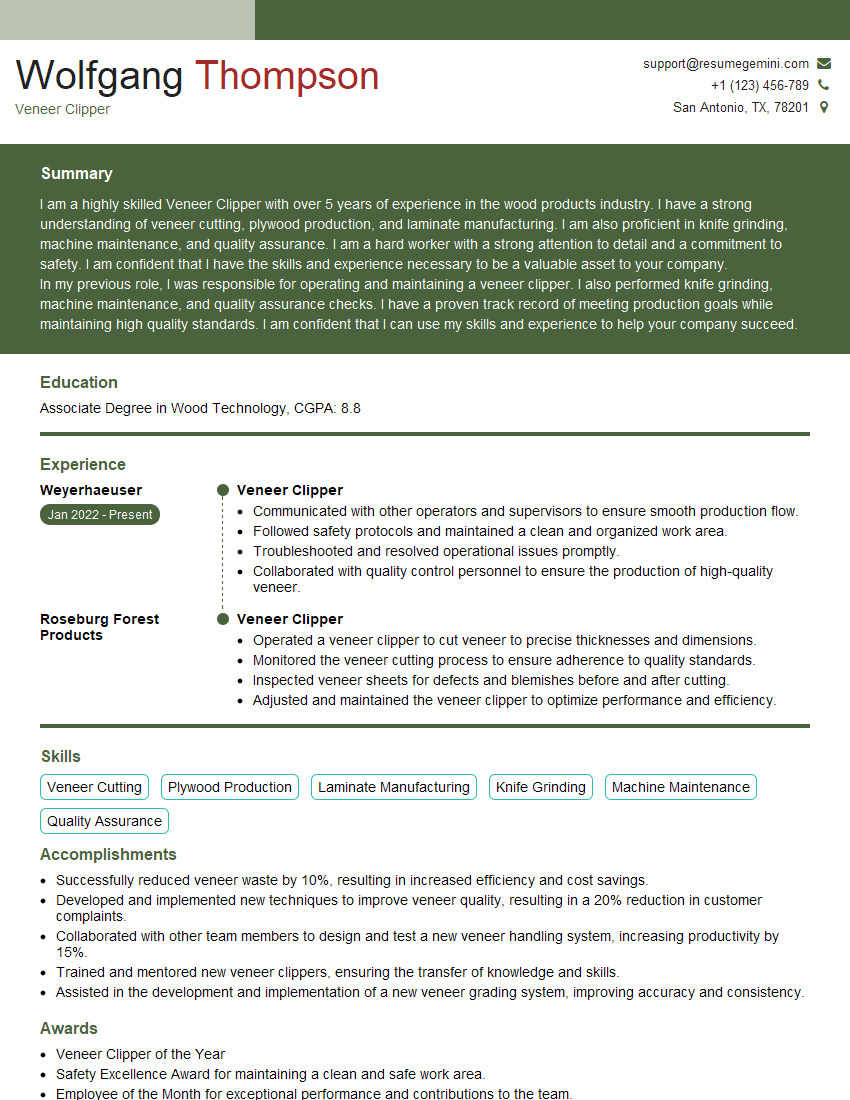
Wolfgang Thompson
Veneer Clipper
Summary
I am a highly skilled Veneer Clipper with over 5 years of experience in the wood products industry. I have a strong understanding of veneer cutting, plywood production, and laminate manufacturing. I am also proficient in knife grinding, machine maintenance, and quality assurance. I am a hard worker with a strong attention to detail and a commitment to safety. I am confident that I have the skills and experience necessary to be a valuable asset to your company.
In my previous role, I was responsible for operating and maintaining a veneer clipper. I also performed knife grinding, machine maintenance, and quality assurance checks. I have a proven track record of meeting production goals while maintaining high quality standards. I am confident that I can use my skills and experience to help your company succeed.
Education
Associate Degree in Wood Technology
December 2017
Skills
- Veneer Cutting
- Plywood Production
- Laminate Manufacturing
- Knife Grinding
- Machine Maintenance
- Quality Assurance
Work Experience
Veneer Clipper
- Communicated with other operators and supervisors to ensure smooth production flow.
- Followed safety protocols and maintained a clean and organized work area.
- Troubleshooted and resolved operational issues promptly.
- Collaborated with quality control personnel to ensure the production of high-quality veneer.
Veneer Clipper
- Operated a veneer clipper to cut veneer to precise thicknesses and dimensions.
- Monitored the veneer cutting process to ensure adherence to quality standards.
- Inspected veneer sheets for defects and blemishes before and after cutting.
- Adjusted and maintained the veneer clipper to optimize performance and efficiency.
Accomplishments
- Successfully reduced veneer waste by 10%, resulting in increased efficiency and cost savings.
- Developed and implemented new techniques to improve veneer quality, resulting in a 20% reduction in customer complaints.
- Collaborated with other team members to design and test a new veneer handling system, increasing productivity by 15%.
- Trained and mentored new veneer clippers, ensuring the transfer of knowledge and skills.
- Assisted in the development and implementation of a new veneer grading system, improving accuracy and consistency.
Awards
- Veneer Clipper of the Year
- Safety Excellence Award for maintaining a clean and safe work area.
- Employee of the Month for exceptional performance and contributions to the team.
- Veneer Quality Control Award for consistently producing highquality veneers that meet customer specifications.
Certificates
- Certified Veneer Clipper Operator (C.V.C.O.)
- National Wood Flooring Association (NWFA) Certification
- Occupational Safety and Health Administration (OSHA) 30-Hour Safety Training
- American National Standards Institute (ANSI) Z244.1-2003 Machine Guarding Standard
Career Expert Tips:
- Select the ideal resume template to showcase your professional experience effectively.
- Master the art of resume writing to highlight your unique qualifications and achievements.
- Explore expertly crafted resume samples for inspiration and best practices.
- Build your best resume for free this new year with ResumeGemini. Enjoy exclusive discounts on ATS optimized resume templates.
How To Write Resume For Veneer Clipper
- Highlight your skills and experience in veneer cutting, plywood production, and laminate manufacturing.
- Demonstrate your proficiency in knife grinding, machine maintenance, and quality assurance.
- Emphasize your commitment to safety and your ability to work independently.
- Showcase your ability to meet production goals while maintaining high quality standards.
Essential Experience Highlights for a Strong Veneer Clipper Resume
- Operate and maintain a veneer clipper
- Perform knife grinding
- Conduct machine maintenance
- Perform quality assurance checks
- Meet production goals
- Maintain high quality standards
- Work safely and efficiently
Frequently Asked Questions (FAQ’s) For Veneer Clipper
What is a Veneer Clipper?
A Veneer Clipper is a machine used to cut thin sheets of wood, called veneer, from logs or flitches. Veneer is used to make a variety of wood products, including plywood, furniture, and musical instruments.
What are the different types of Veneer Clippers?
There are two main types of Veneer Clippers: rotary clippers and slicing clippers. Rotary clippers are used to cut veneer from round logs, while slicing clippers are used to cut veneer from flitches.
What are the different types of veneer?
There are many different types of veneer, including hardwood veneer, softwood veneer, and decorative veneer. Hardwood veneer is made from hardwoods, such as oak, maple, and cherry. Softwood veneer is made from softwoods, such as pine, fir, and spruce. Decorative veneer is made from a variety of woods, including exotic woods and figured woods.
What are the different uses of veneer?
Veneer is used to make a variety of wood products, including plywood, furniture, and musical instruments. Plywood is made by gluing thin sheets of veneer together. Furniture is made by veneering wood frames with thin sheets of veneer. Musical instruments are made by veneering wood bodies with thin sheets of veneer.
What are the different grades of veneer?
Veneer is graded according to its quality. The highest grade of veneer is A grade, which is free of defects. The lowest grade of veneer is D grade, which has a number of defects.
How is veneer applied?
Veneer is applied to wood frames using a variety of methods, including gluing, pressing, and vacuum pressing. Gluing is the most common method of applying veneer. Pressing is used to apply veneer to curved surfaces. Vacuum pressing is used to apply veneer to large surfaces.
How is veneer finished?
Veneer is finished using a variety of methods, including sanding, staining, and painting. Sanding is used to smooth the surface of the veneer. Staining is used to change the color of the veneer. Painting is used to protect the veneer from wear and tear.
What are the different types of veneer products?
There are many different types of veneer products, including veneer sheets, veneer panels, and veneer overlays. Veneer sheets are thin sheets of veneer that are used to make plywood and furniture. Veneer panels are made by gluing together several layers of veneer. Veneer overlays are thin sheets of veneer that are used to cover existing wood surfaces.